Since gaining a bit of a reputation locally for being the guy who makes “Character bows”, I’ve been “gifted” rather a lot of “character staves”! And not wanting to appear ungrateful, I’ve become prone to accepting these staves, rather than politely declining the “generous” offer of yet more firewood!
Actually, once in a while, some of these typically low diameter branch staves don’t look too bad, (at least upon initial inspection) and the bow featured in this post was built from one such branch stave which was donated to me in 2022.
Despite the low diameter and general knottiness of this particular branch stave, there was one face which looked quite nice and could make for a sound back. So other than a couple of branch whirls to deal with on the belly side, I could easily envisage making a simple but effective primitive bow from this stave. So in the spring of 2024 I set to work on it.
Roughing out was straight forward enough and I was pleased to get past all the pith without running low on heart wood material. I decided to keep the face profile fairly narrow so as to minimise the amount of sapwood which was curling around the edges towards the belly due to the low diameter and high crown on the back.
The stave was fairly straight other than a tiny amount of deflex right in the middle where I’d lay out a stiff handle with fades. I decided to leave this deflex alone since I only had 62″ of overall length to work with, and really hoped to get 27″ of draw length out of this bow. I figured that lightly flicked tips could possibly work since the deflex in the handle would help cushion the extra strain that any reflex might place on the relatively short working sections of the limbs. Flicking the tips would help reduce any stack experienced which might result from the short length.
A stiff 4″ handle with 3″ fades, and 5″ stiff tips would reduce the overall working sections of both limbs down to around 20″, which isn’t a great deal to support the load that a 27″ draw would place on a bow as short as this one. So after roughing out and steaming the tips into a light reflex, I decided to sinew back this stave and leave her to cure out over the summer of 2024.
By early autumn the sinew backing appeared to be thoroughly cured and a little bit of overall reflex had been drawn into the stave as the sinew had shrunk down tight. This often happens when enough sinew is used, which is why I typically apply my sinew backings by weight to ensure enough (but not too much) sinew is applied.
I find that a total of 3 ounces of sinew (an ounce and a half of dry processed sinew per limb) is the perfect amount for a bow in the 58 – 64″ range. 3 oz is plenty enough sinew to add significant extra power and resistance to set, but not so much sinew that the added weight of the sinew starts to add power robbing mass to the limbs.
I find that more than 3oz of sinew on a bow this length crosses the point of diminishing returns, and the extra weight the additional sinew gives to the limbs can actually start to decrease arrow speed and create a fair bit of limb vibration too. This vibration post string release is typically felt as an uncomfortable form of hand shock. So when it comes to sinew backing a bow, more is not necessarily better!
So 3oz of dry sinew is about perfect, so long as the bulk of its distribution is along the working sections of the limbs, as opposed to the handle section or the last 6″ of the tips, which will not be improved one bit by the added weight of a full thickness layer of sinew. In fact the tips really only want as thin a layer of sinew as is possible. Just enough to cover the visible surface of the back. Enough to add structural integrity but not weight.
The stave was brought into shape and a rounded D shaped belly was chosen so as to get as much sap wood off the belly corners as possible. This allowed for the retention of as much heart wood as possible and resulted in an overall ratio of around 50/50 sapwood/heartwood. Which was pretty good for a low diameter branch stave.
Three of the small knots presenting on the belly were a bit weak looking so I opted to dig them out and fill them with a mixture of epoxy and yew dust so as to add back some strength whilst retaining as best a natural look as possible.
Before putting the long string on for the first few pulls the stave held about 2″ of overall reflex, but I new that a fair bit of that overall reflex would disappear once the tillering got well underway. And as expected, by the time 26″ had been reached the overall reflex had reduced to about an inch. My expectation was for it to drop another inch by the time full draw was reached and the bow had been properly shot in, and my expectation was spot on.
So after a thorough shooting in period, the overall reflex/deflex reduce to about neutral, which was ideal for a bow which was going to end up only 60″ nock to nock. The light reflex in the tips had held it’s shape, even with their relatively low diameter, and the 1/4″ positive tiller had stayed true throughout the shooting in period.
46# at 27″ was about right for a stave of this nature and she was pleasant to shoot too. So to finish her up I fitted her up with a pair of red deer antler tip overlays. To decorate the back I fitted a nice King Rat snake skin which I had squirreled away. As well as looking quite cool, I also like that snake skins are pretty water resistant and afford a sinew backing quite a bit of extra protection from water/humidity ingress, which is always a bonus in a humid country like ours!
This snake skin wasn’t long enough to run tip to tip so I left the tips bare to show off the sinew backing. The transition from the snake skin to the sinew at the tips was wrapped with deer back strap sinew to tidy up the termination of the snake skin. The snake skin and the sinew wrappings were then edged with a black paint made from my local black earth pigment (Bideblack) mixed with hide glue. And the cream coloured dots added to the black painted boarder were made from mixing hide glue with deer bone dust.
The bow was finish and sealed thoroughly with 8 coats of danish oil made satin in appearance through a final pumice polish buffed down with wax paste. I opted to cover the slightly contoured handle with a nice piece of my home bark tanned red deer leather in a nice natural red tan colour, laced up with some leather lace cut from a roe deer hide I bark tanned last year.
The arrow pass is a piece of red deer shin leather which I tanned with some of the hair still on. It’s a bit like a rustic primitive version of the calves hair leather pieces you can buy from archery shops, only cooler!
I really enjoyed building this bow and found her to be really pleasurable to shoot. The chrono consistently recorded speeds of around 150ft/sec from a 400 grain arrow which is quite reasonable for a character branch stave.
The balanced tiller and flicked low mass tips helped mitigate any hand shock and the slightly contoured handle made for a nice comfortable grip. I can imagine this bow giving someone many years of enjoyable and reliable shooting so will be offering this bow for sale in my Southmoor Bows Etsy shop, the listing can be found here:
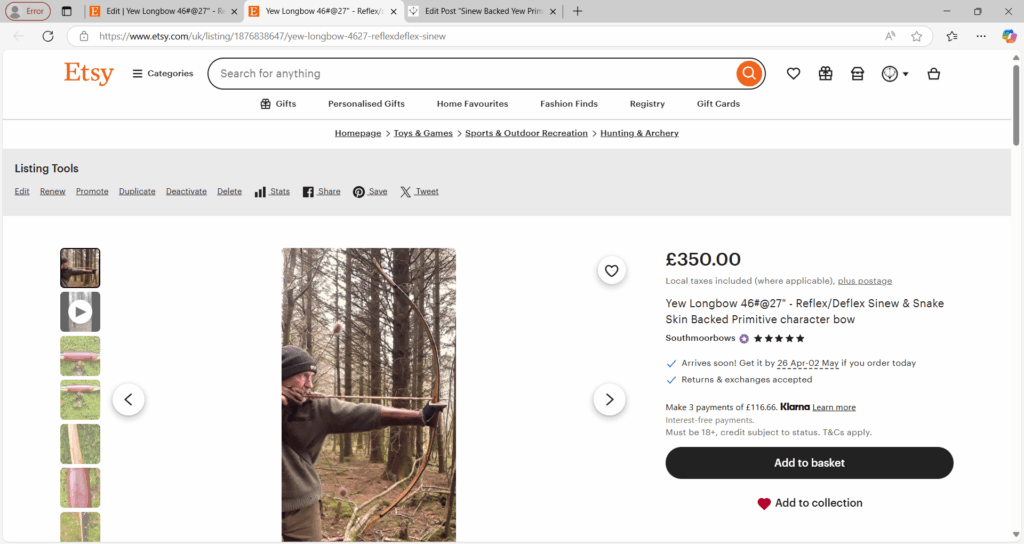
Specifics are as follows:
Draw Weight: 46lbs at 27”
Mass: 725 grams
Length NTN: 60”
Width: 1 3/8” at widest part
Tips: 5” working 3/8” wide at the nocks.
Back: Moderately crowned with undulations with a pyramidal face profile.
Belly Profile: Working limb sections D shaped, transitioning at the tips to ridged shaped cross section.
Tiller: Elliptical. 1/8” positive
Brace height: 5 1/2″
Here she is, hope you enjoy!




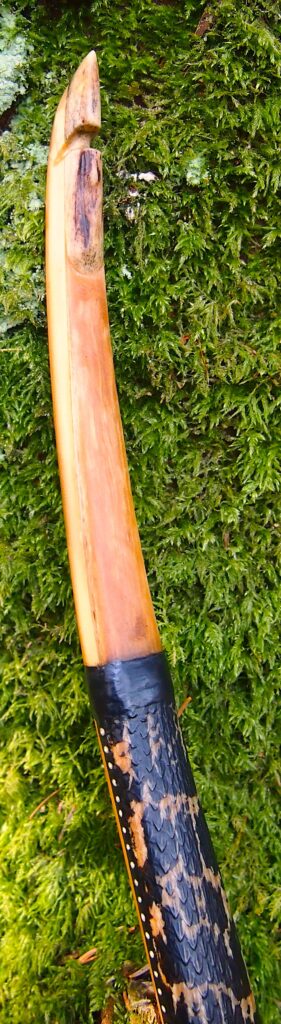
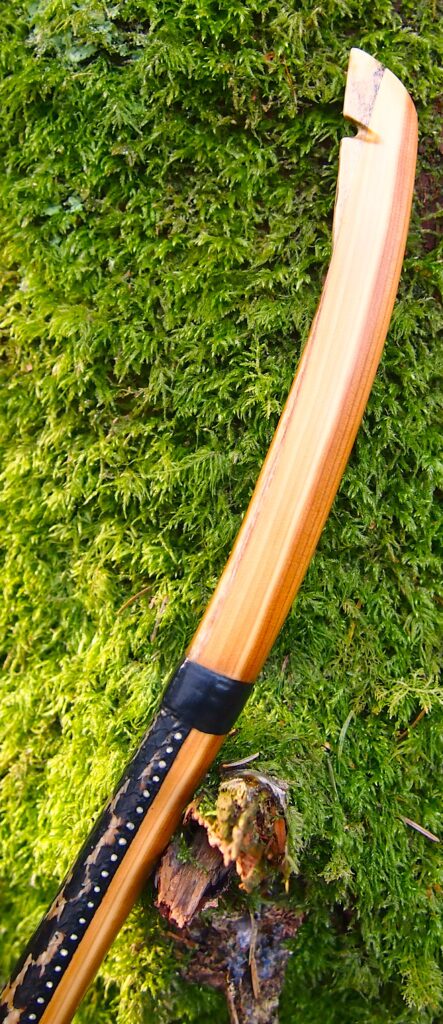
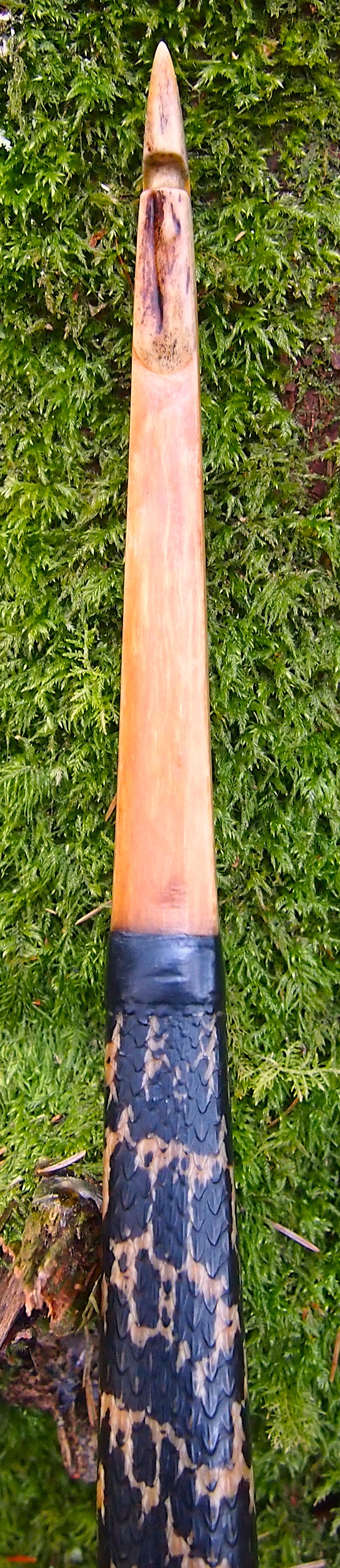
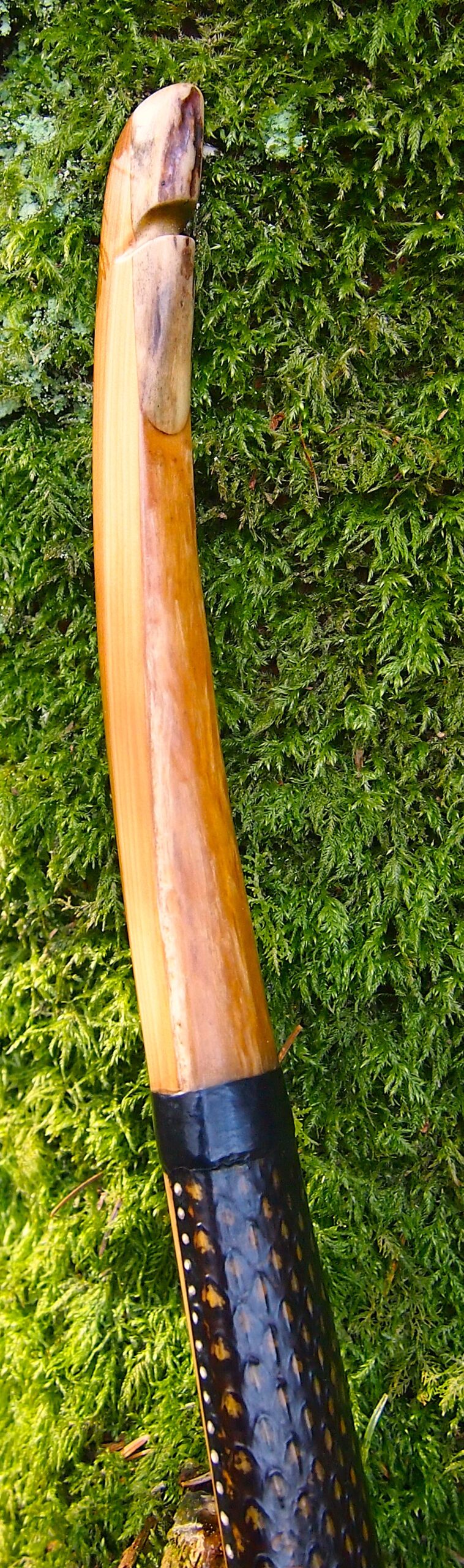
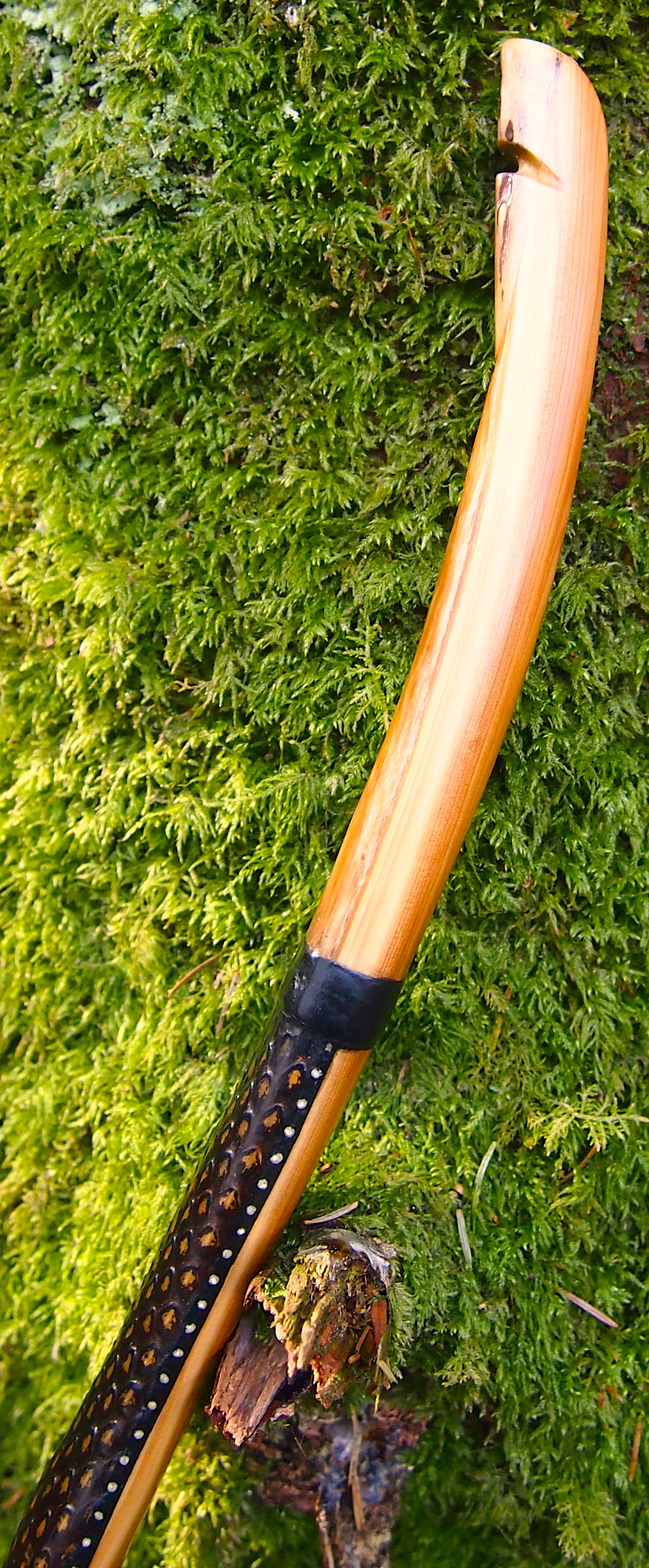
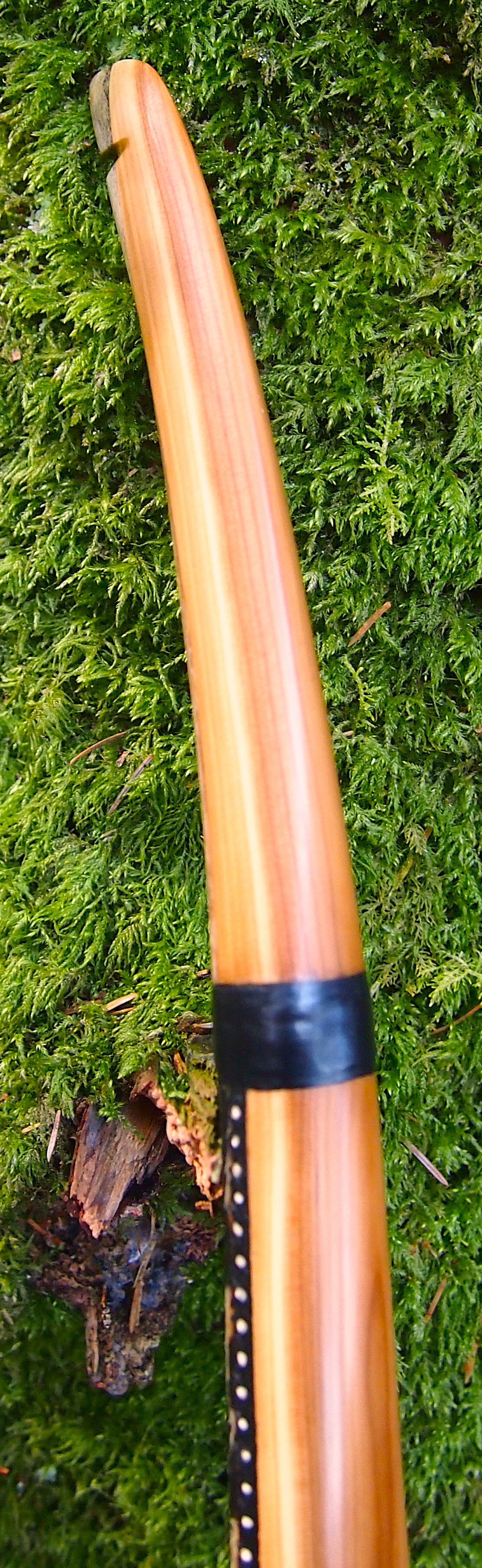
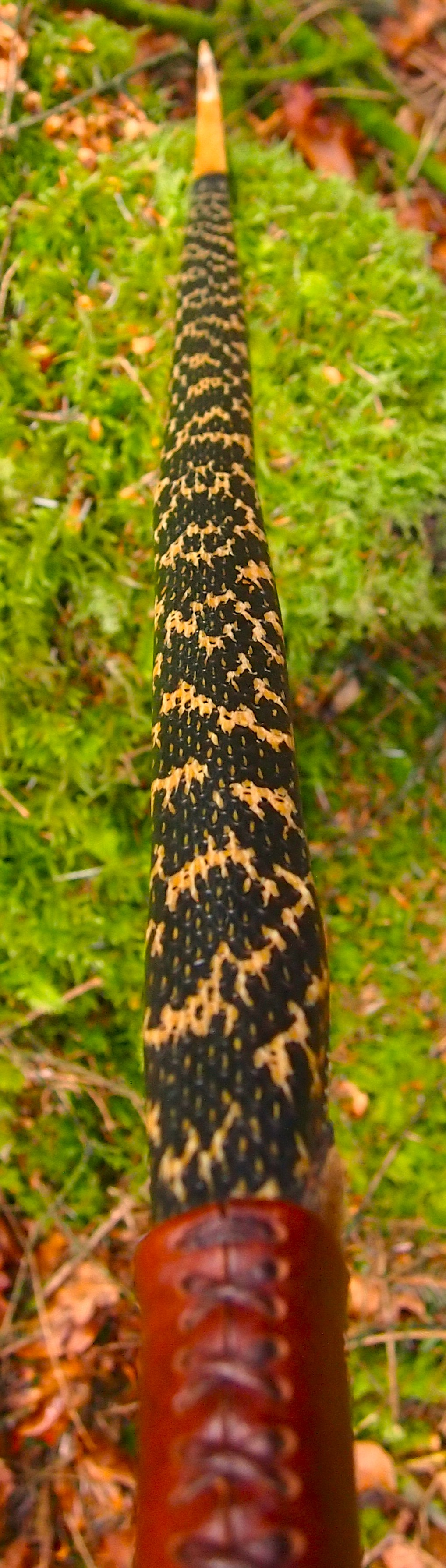
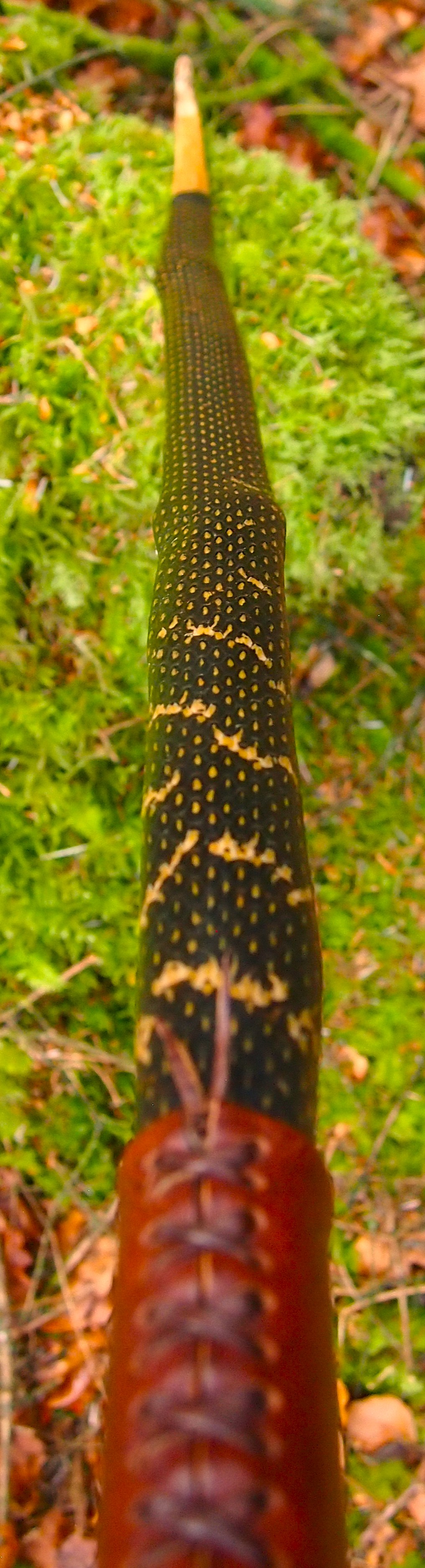
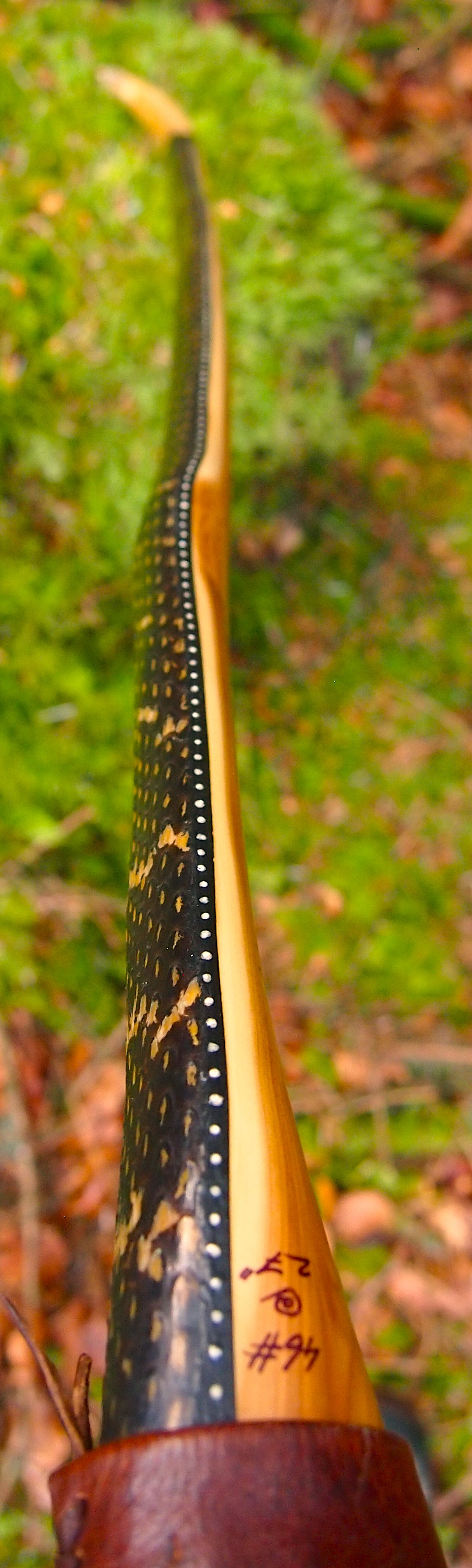
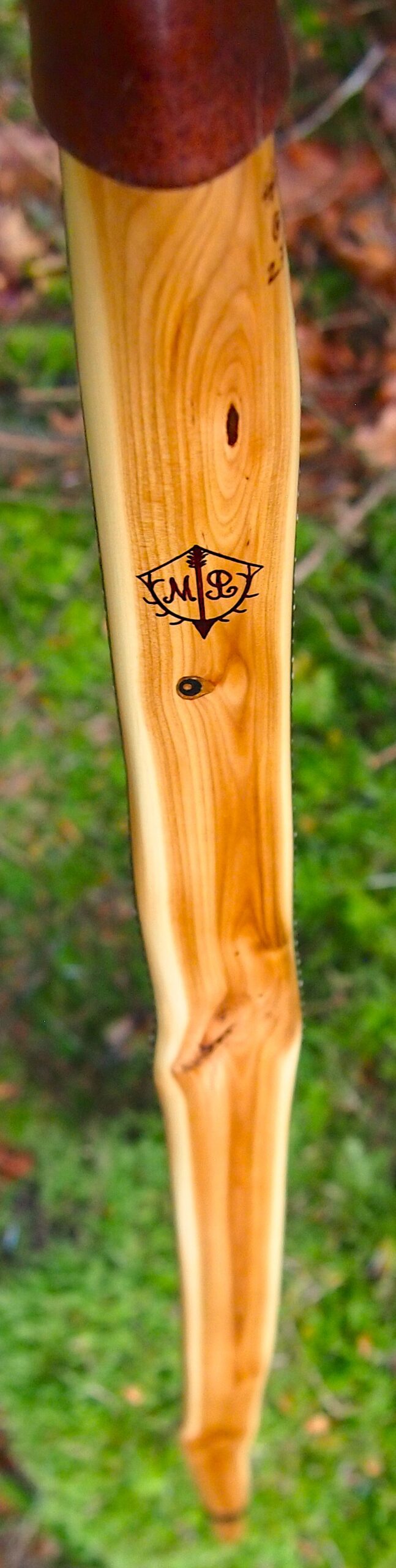
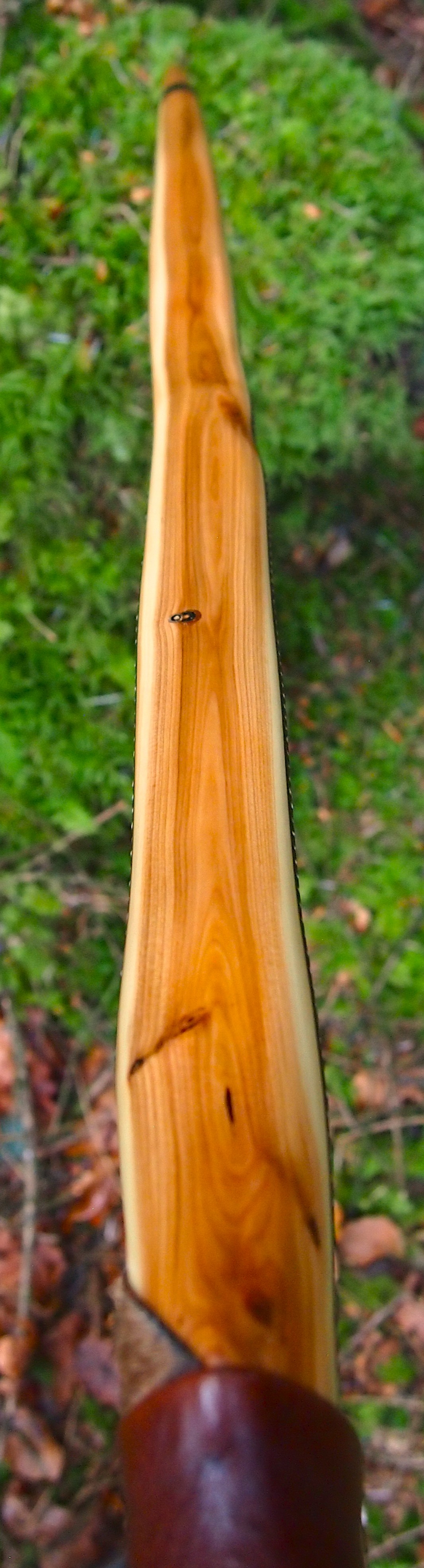
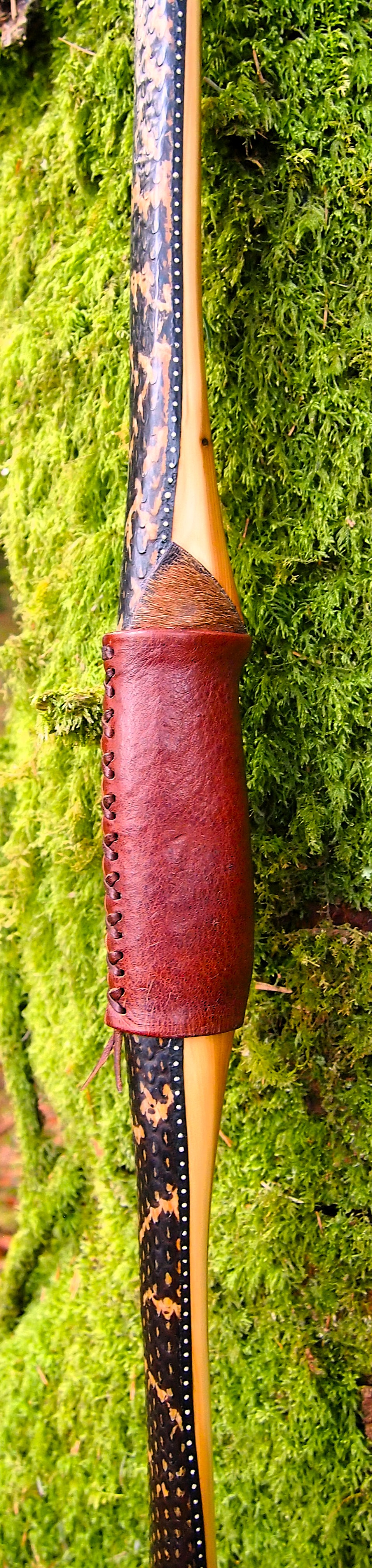
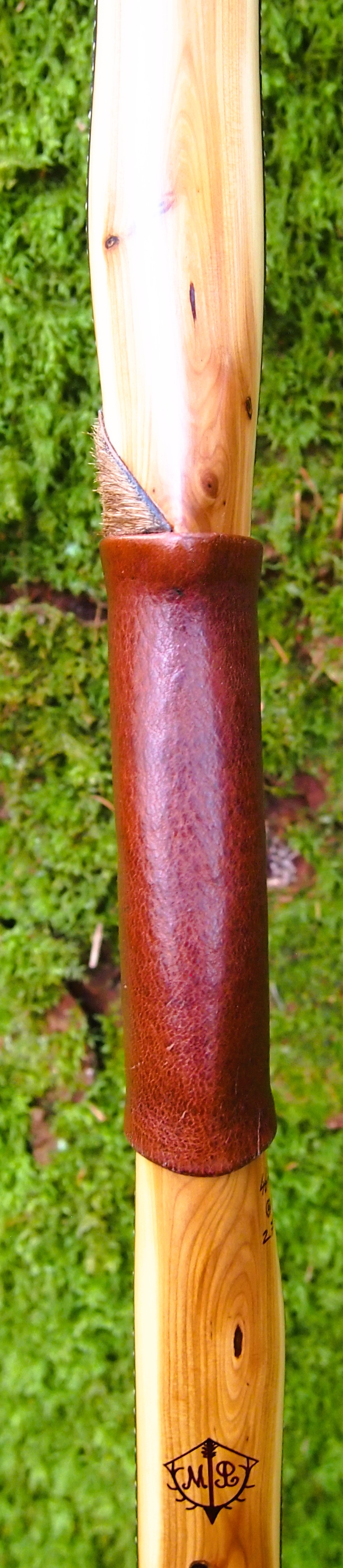
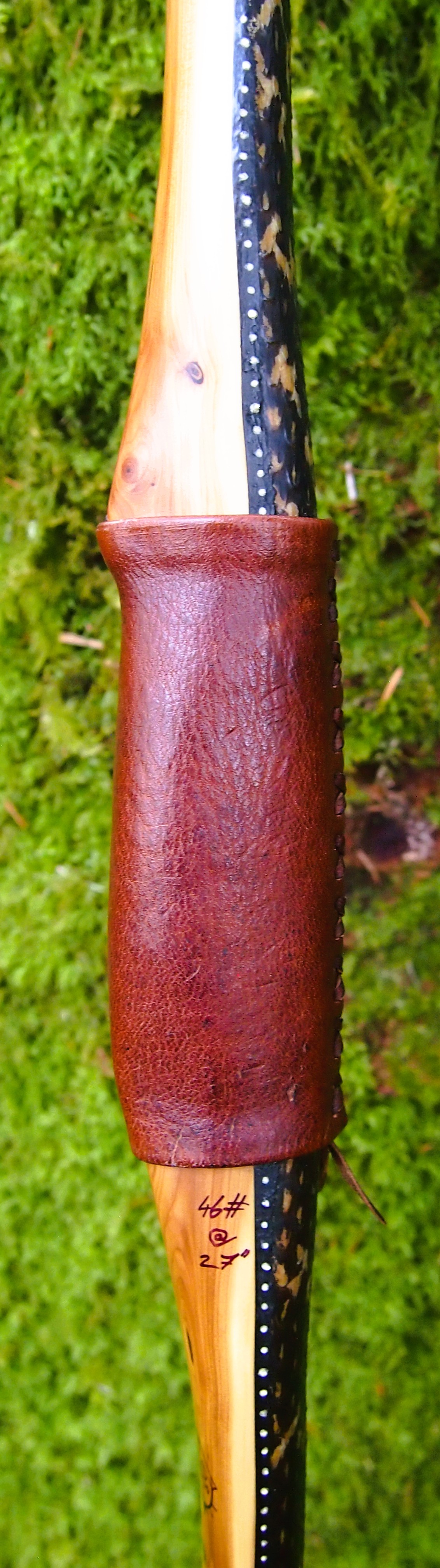
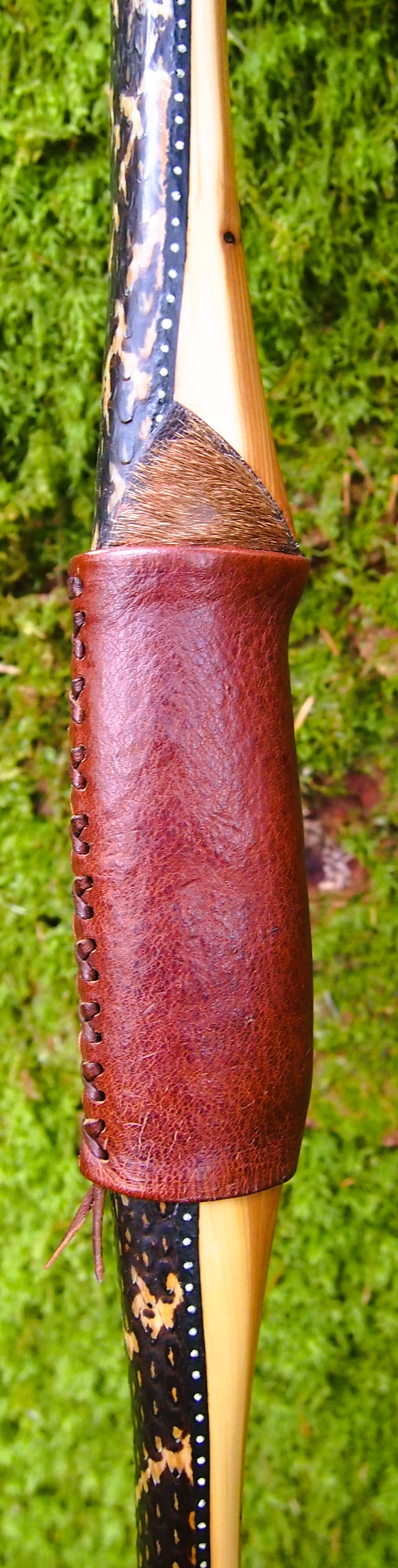
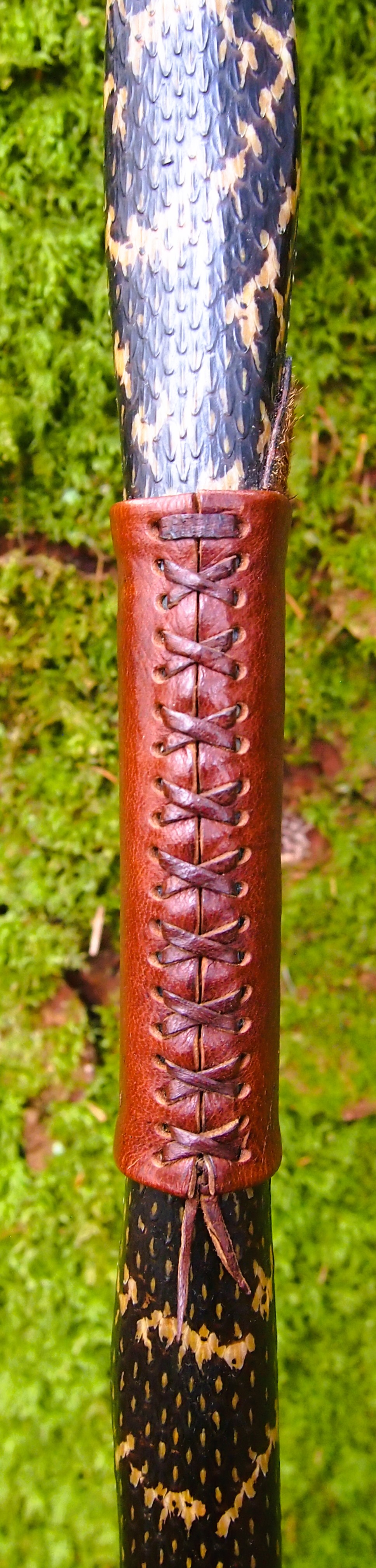


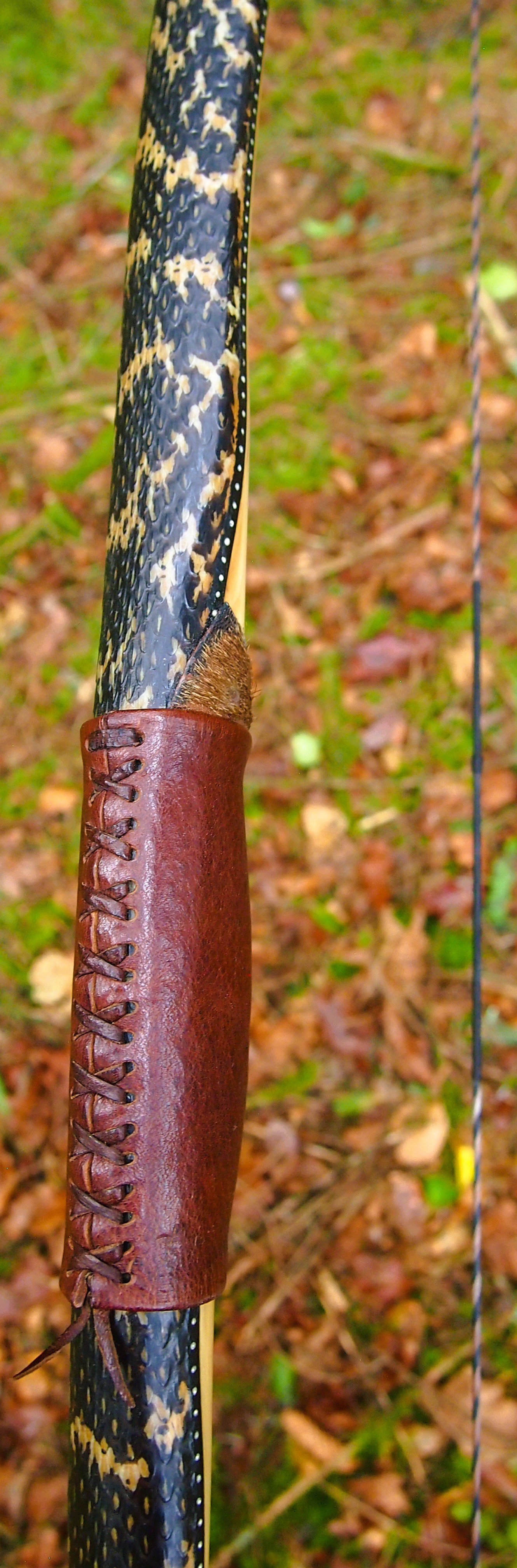




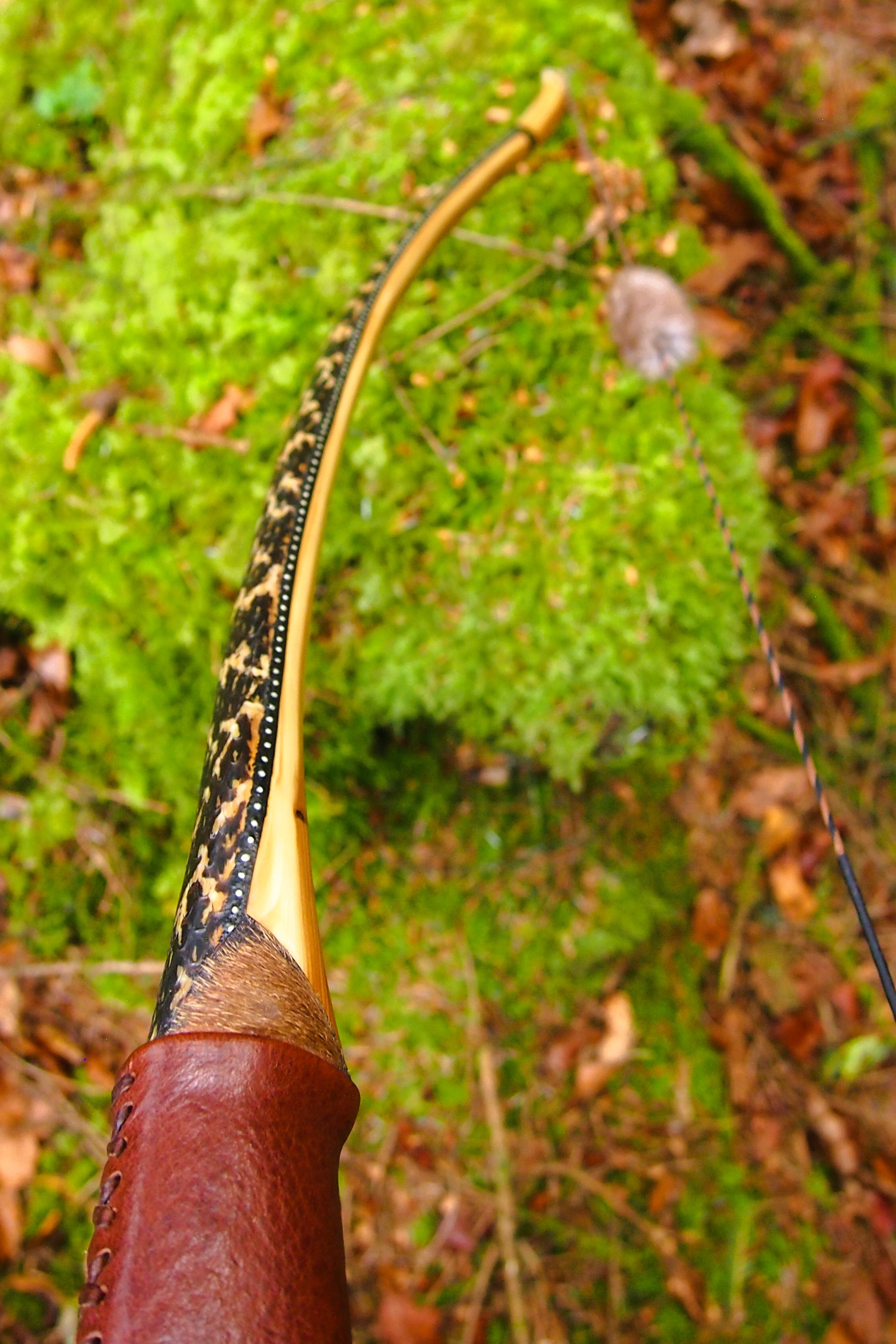
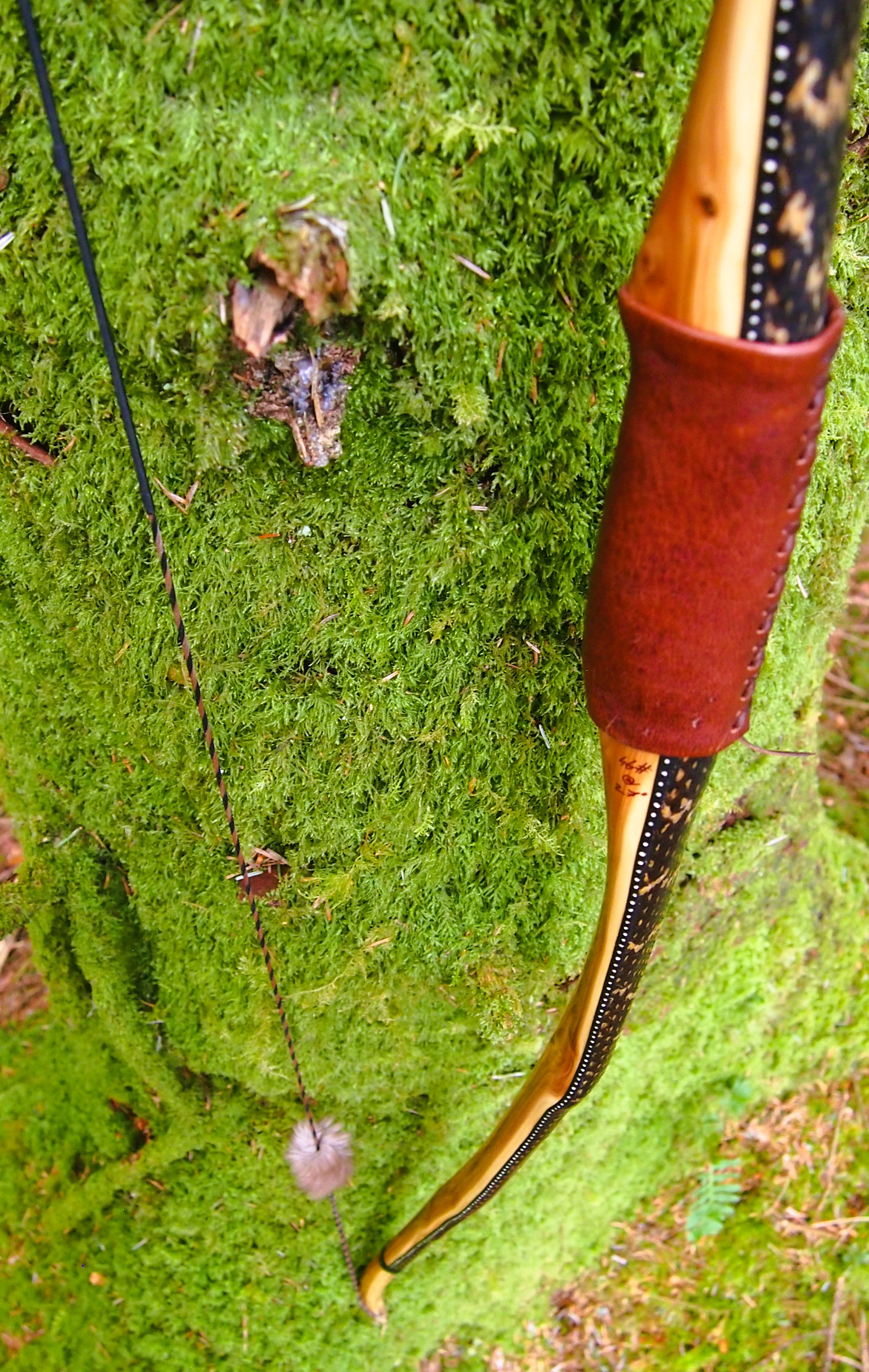
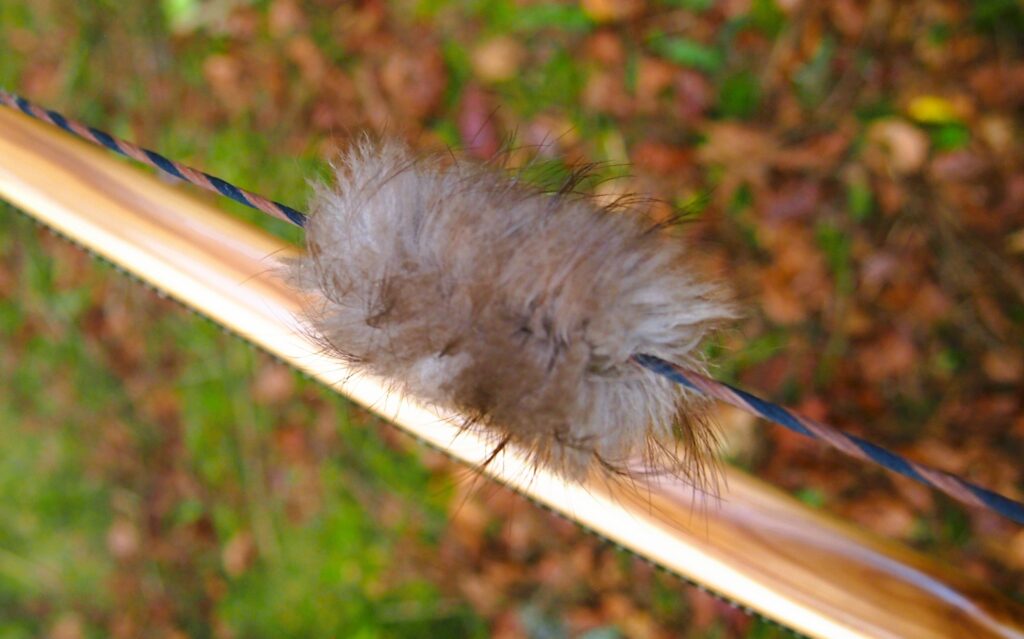
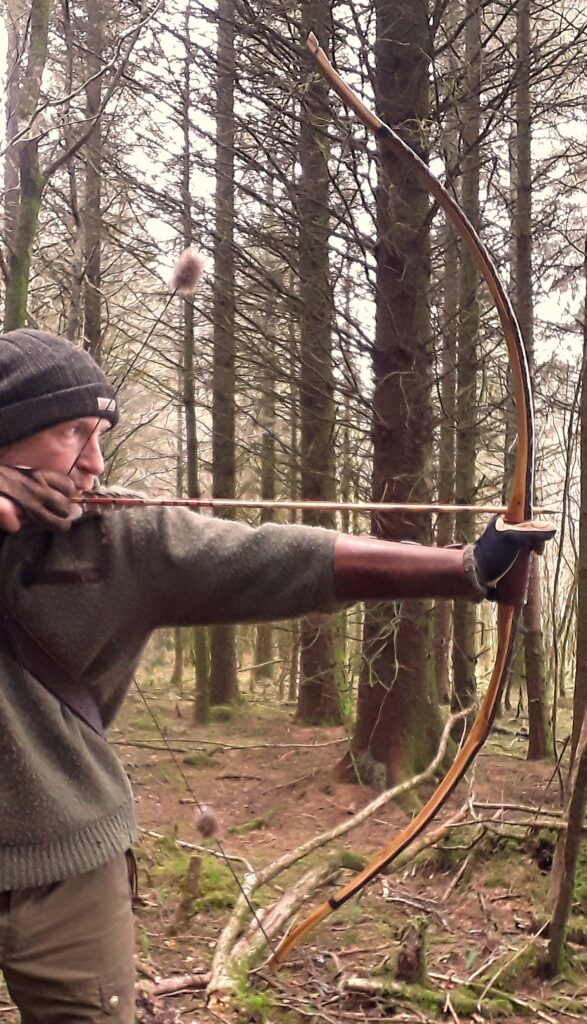